Robotic architecture isn’t just a possibility, it’s inevitable. The question only remains, what other changes will it bring?
The design and assembly process of this thesis can be used to help diagram how to design outside the modular standards of traditional construction and go beyond what is, quite literally, humanly possible.
Site
In order to properly exhibit the potential of new, robotic, architecture. I elected to re-envision Cincinnati's riverfront arena.
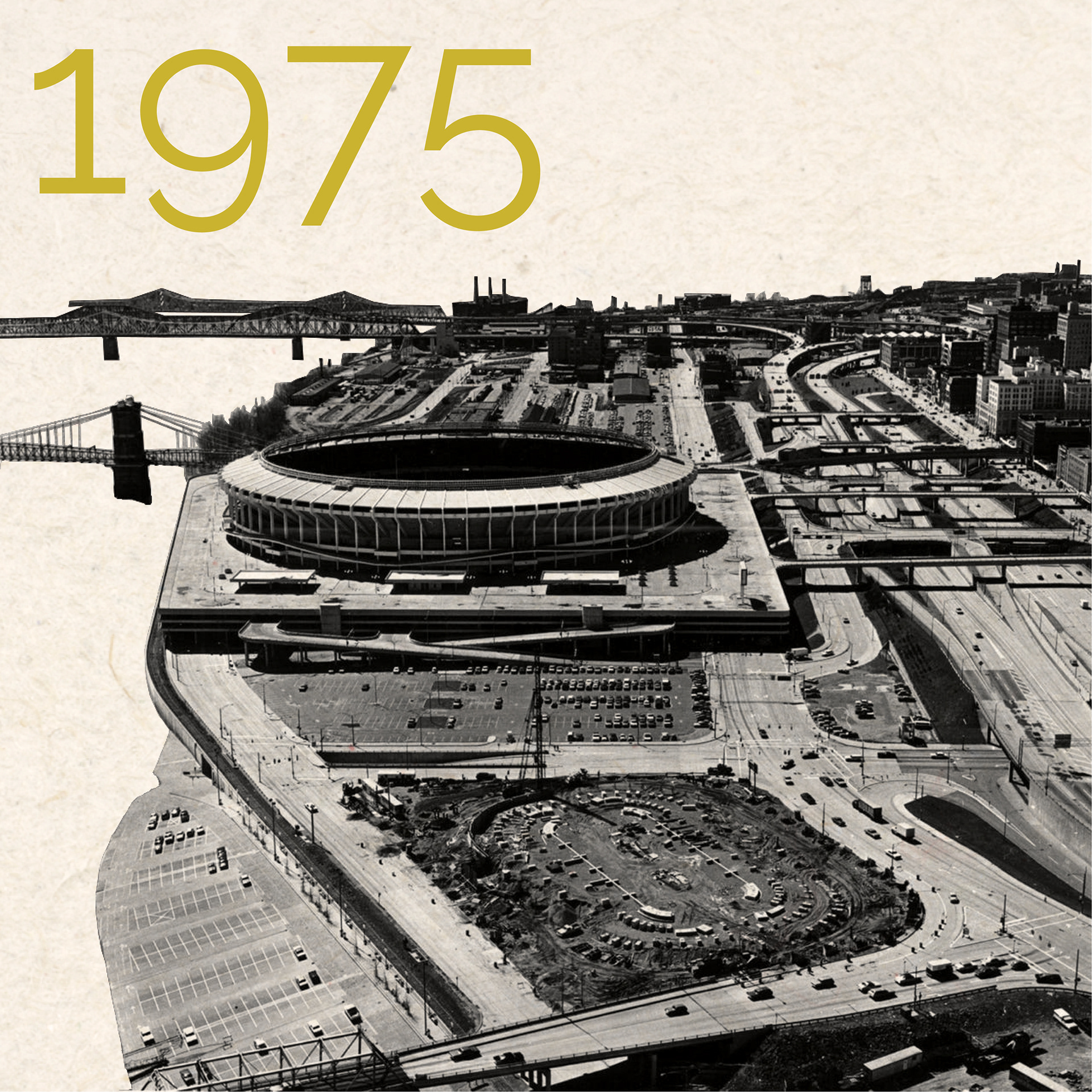
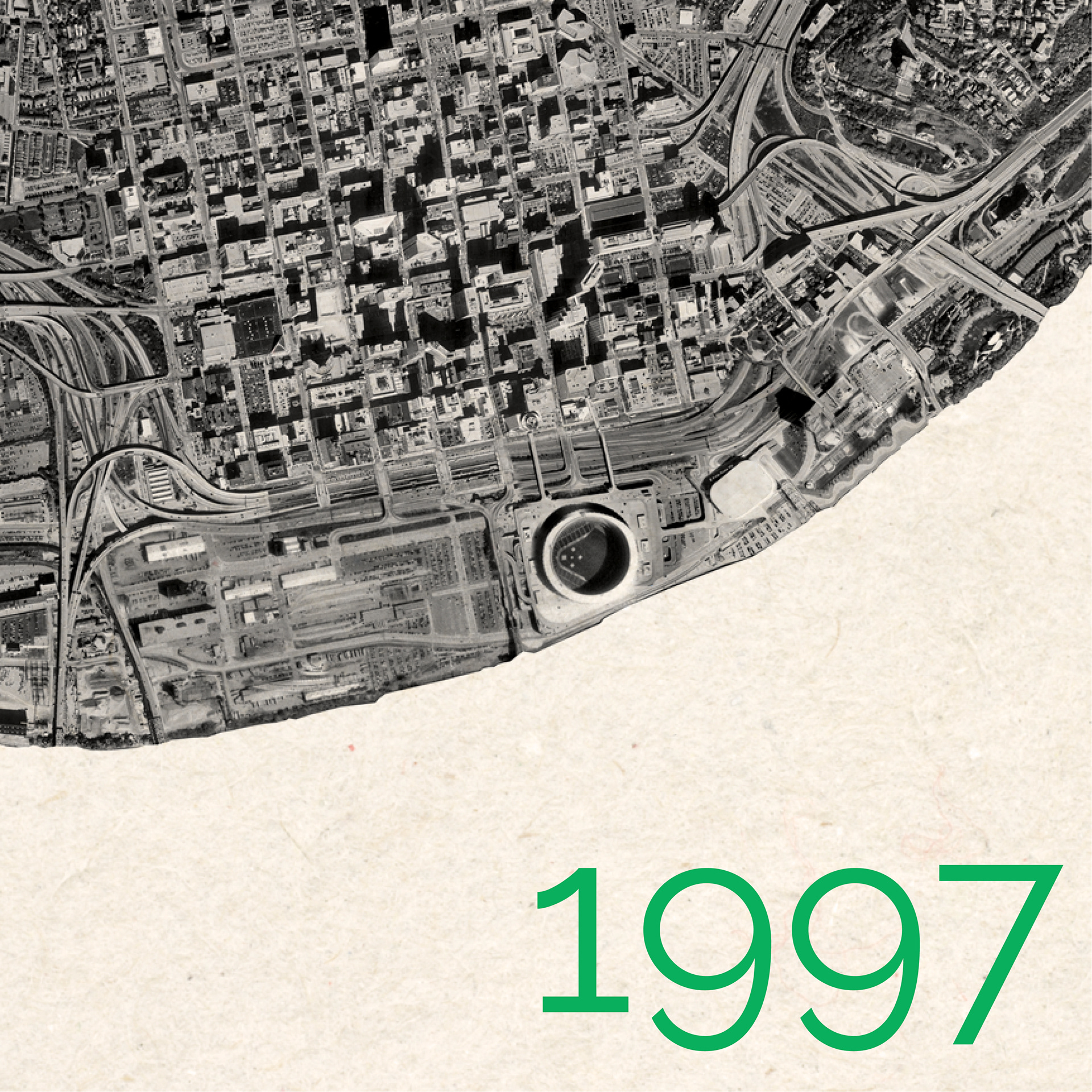
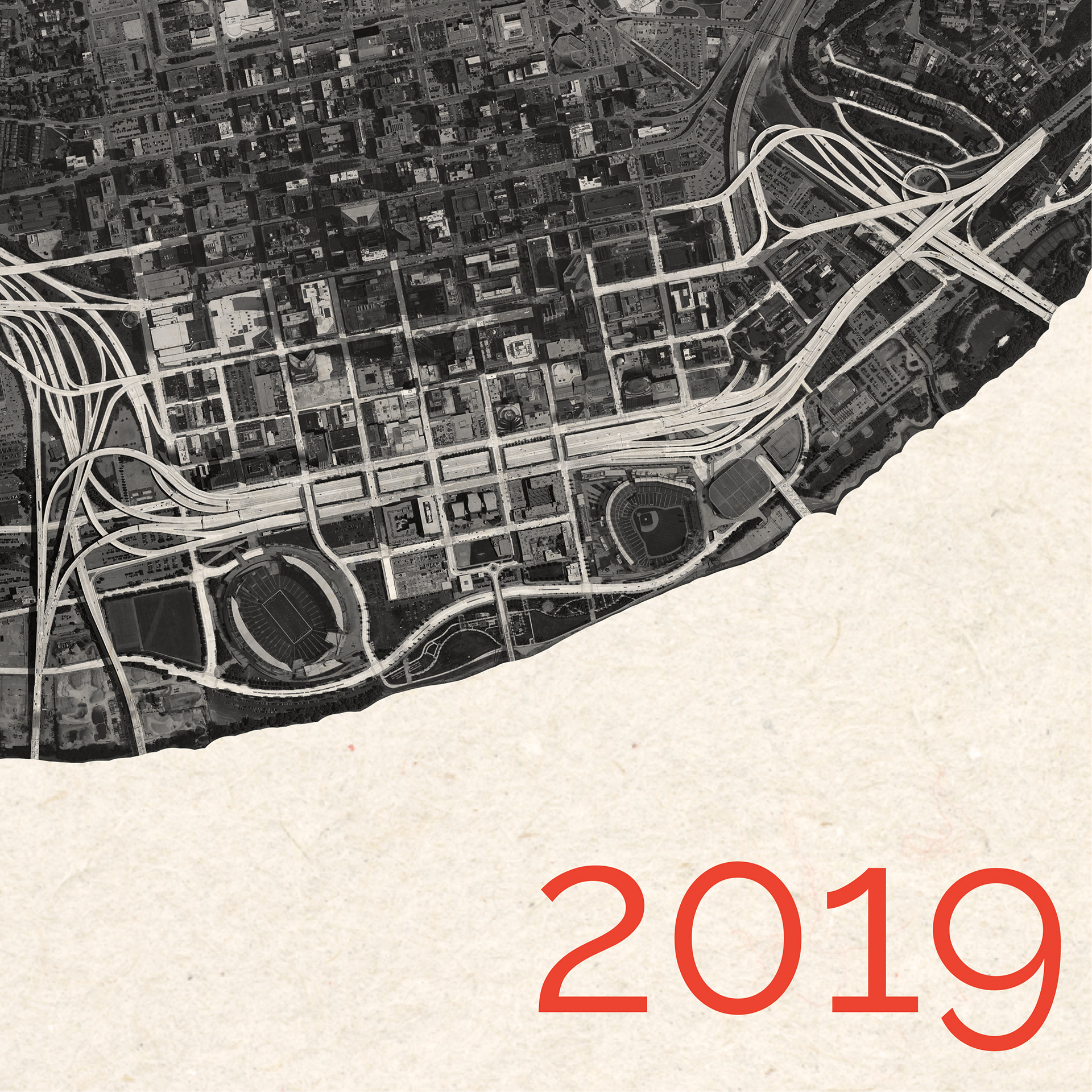
Currently named Heritage Bank Center, the arena constructed in 1975, it remains the untouched bookend to Cincinnati's downtown waterfront. Last renovated in 1997, it has become outdated, unwelcoming and scarred by tragedy.
Design - Interior
My design looked to strip down the building to its lower bowl, expand its structure to include two new seating levels and provide multiple, wider concourses, and introduce access and activity to street level.
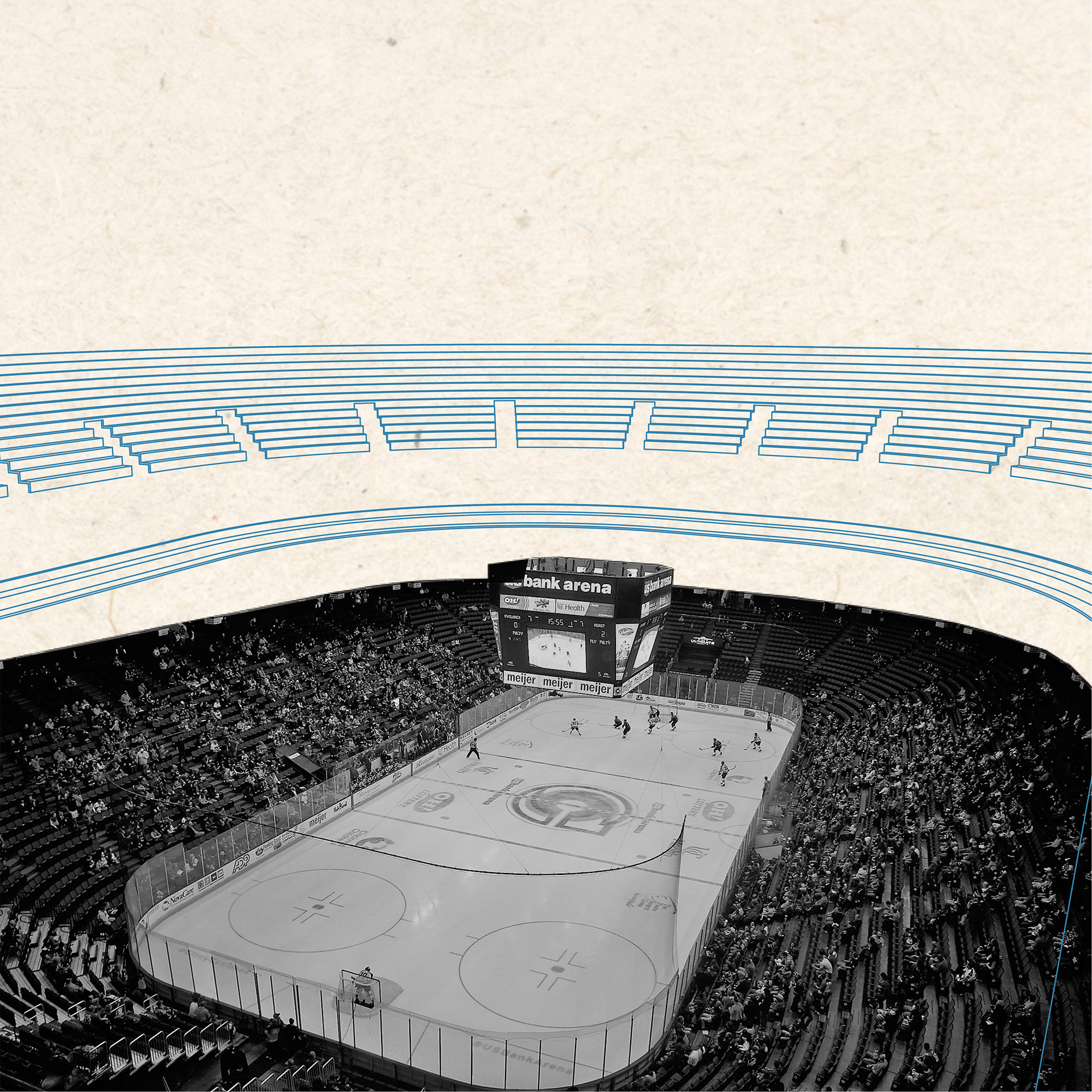
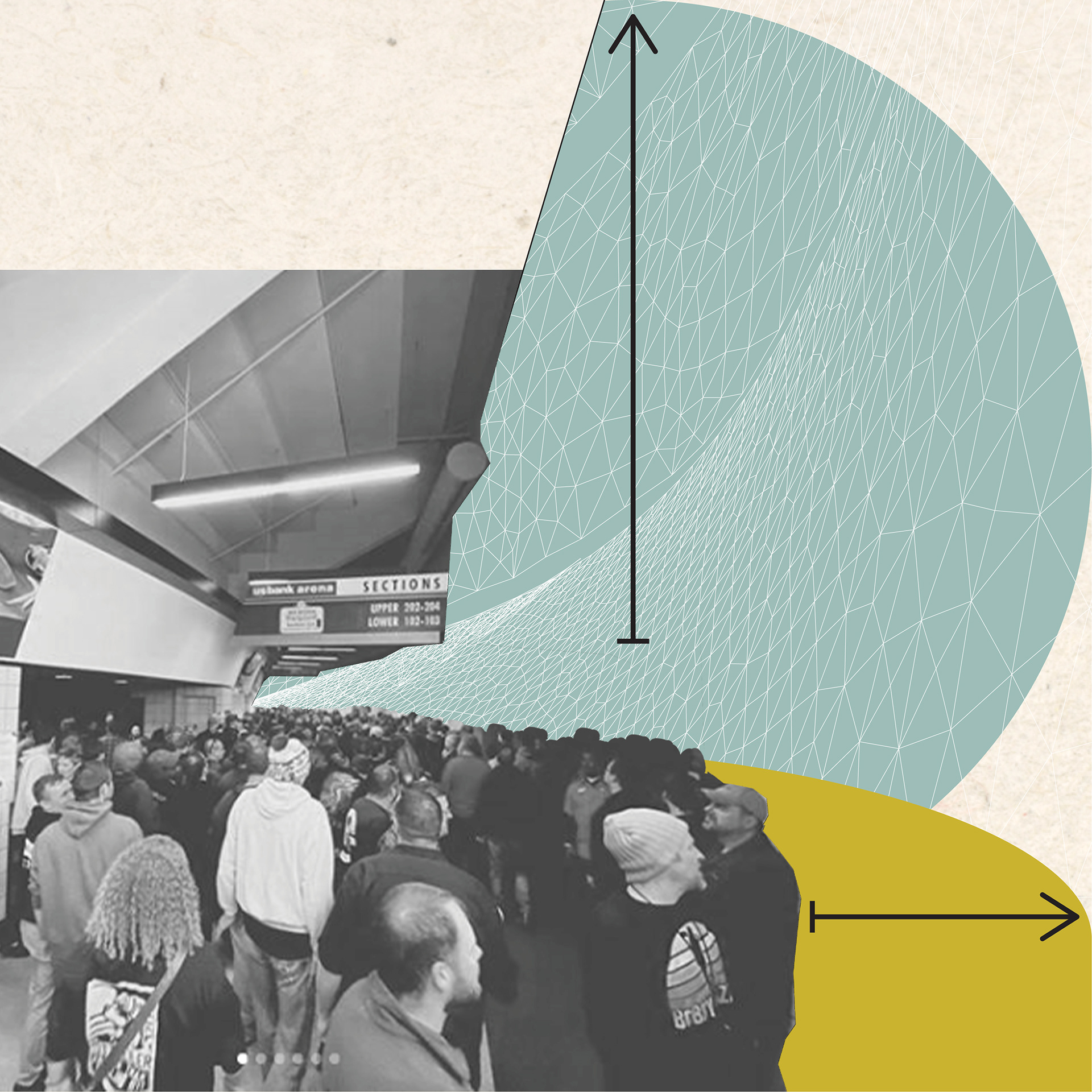
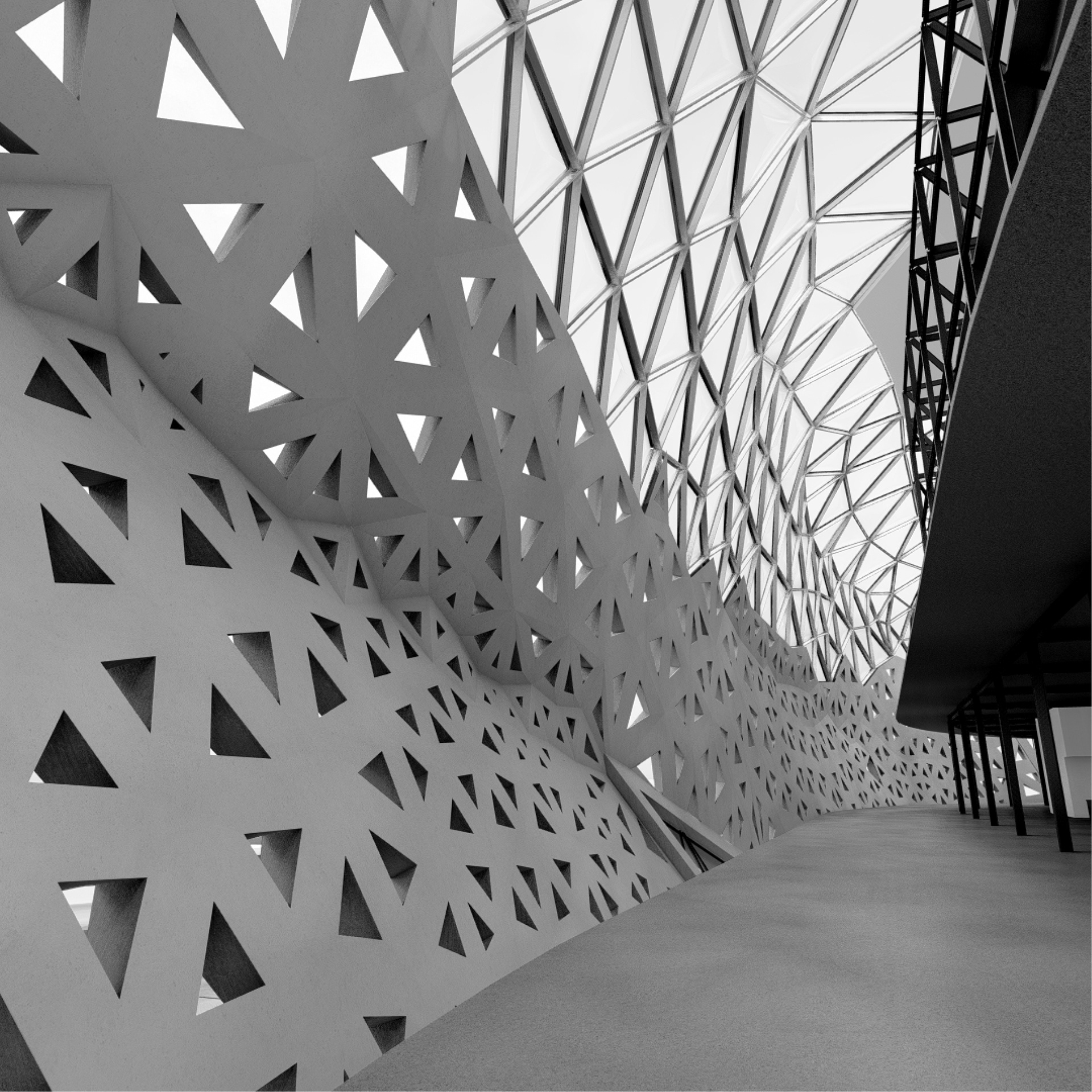
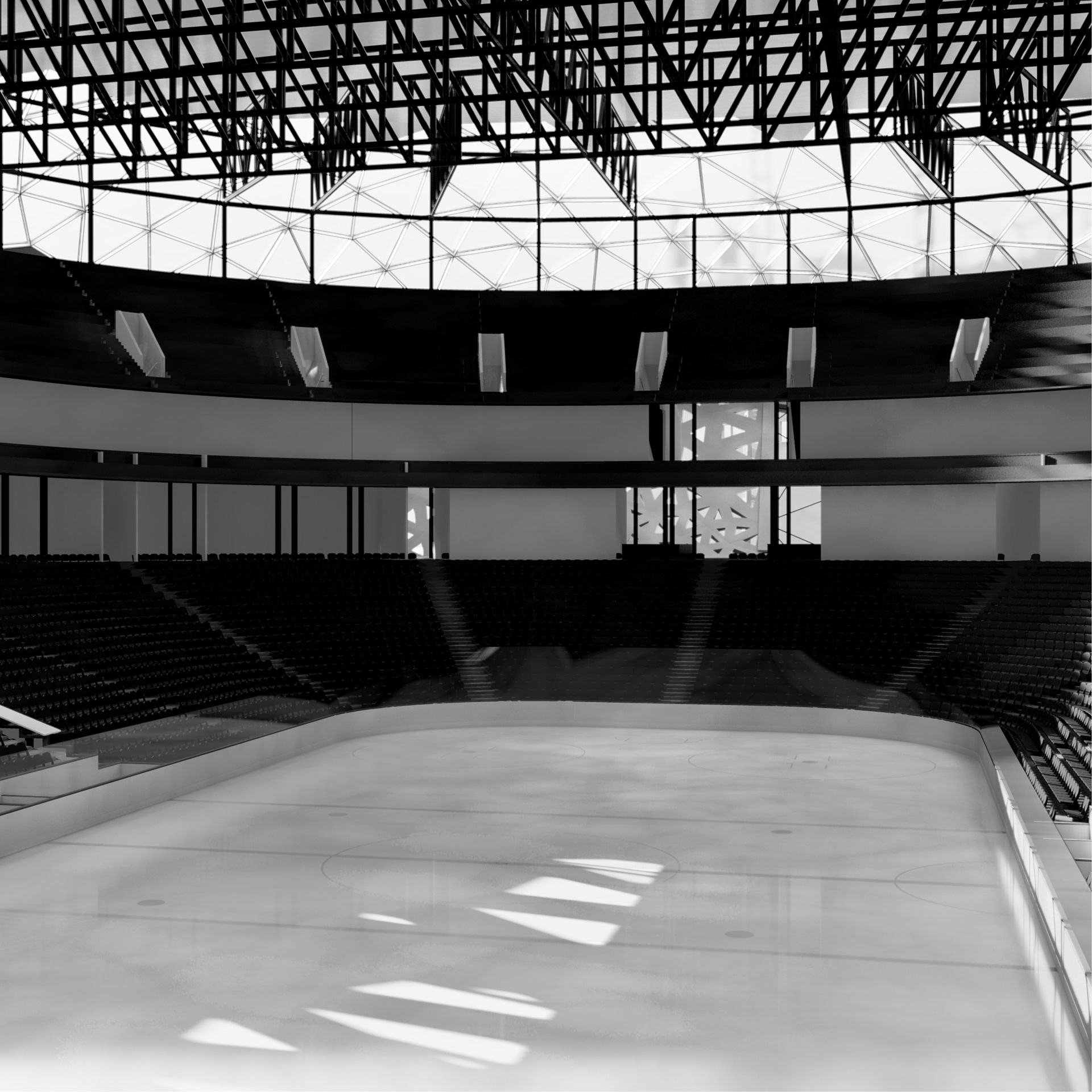
This strategy, along with the internally loaded program, allows for the buildings exterior to develop independently of its interior, making it the ideal canvas to diagram the potential of robotically driven architecture.
Design - Exterior
Modular approach
Modularity in robotics has a different meaning to the of traditional fabrication. Where traditionally modular would mean a unit is uniform in fabrication, material, scale shape and mass. In robotics the requirement for modularity is only limited in fabrication.
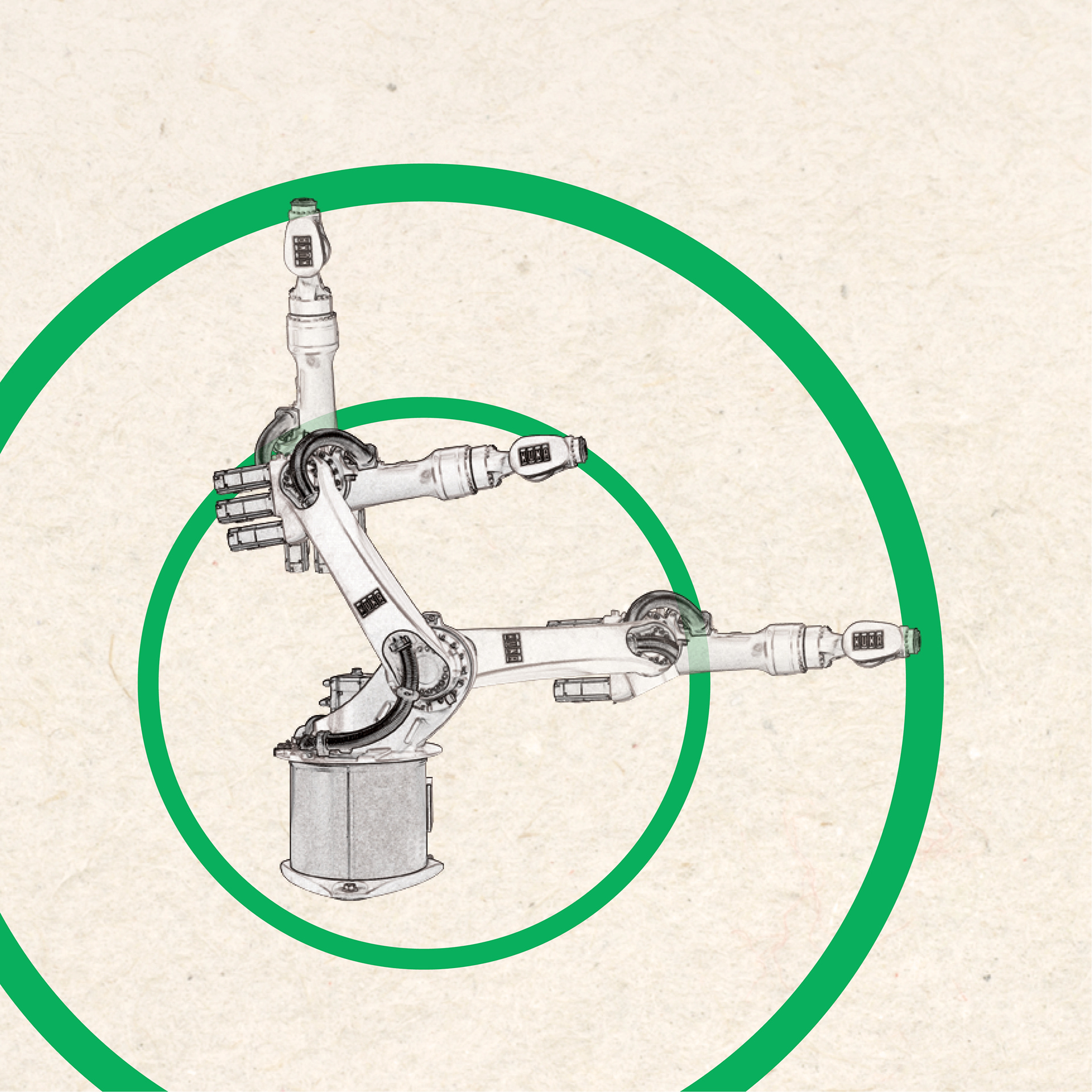
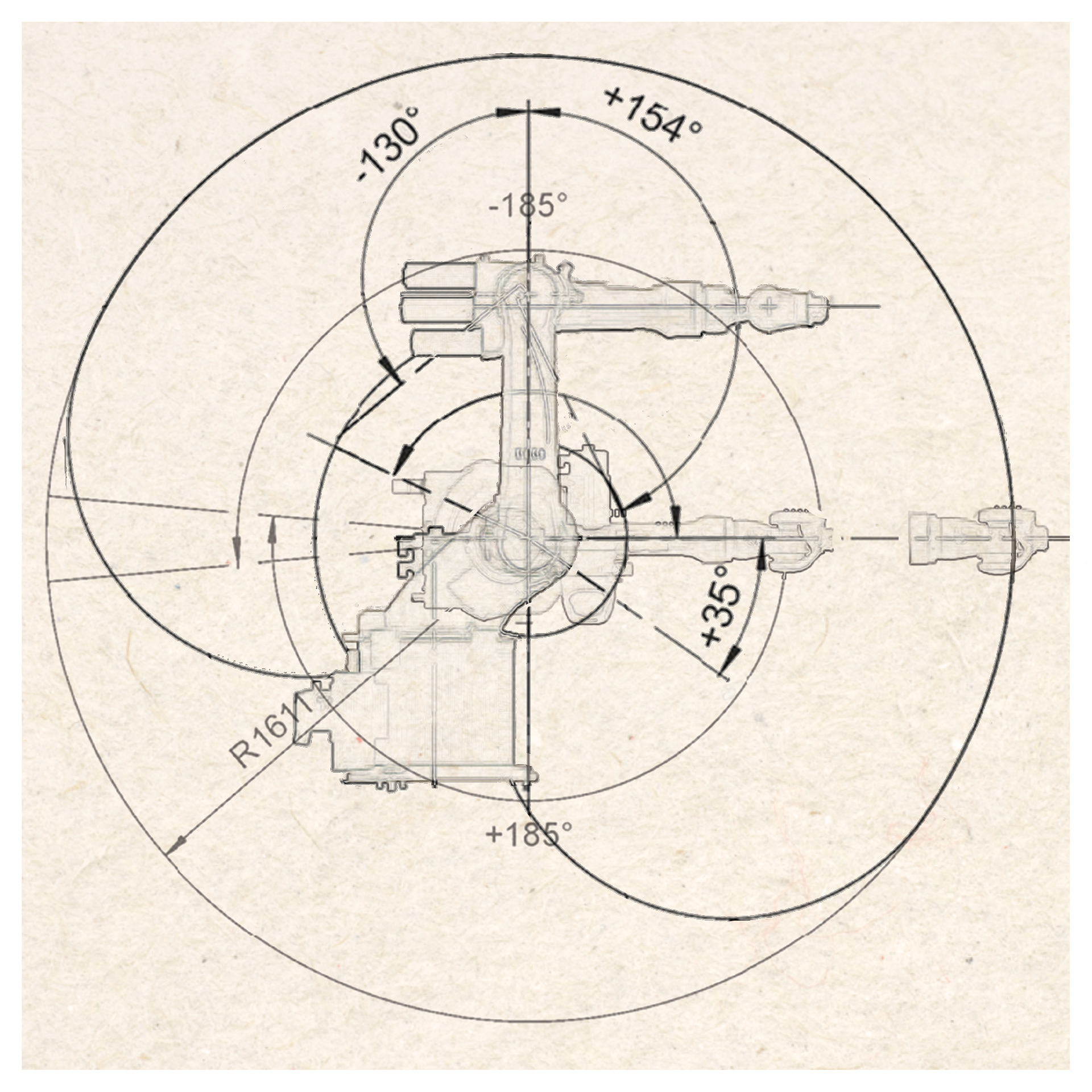
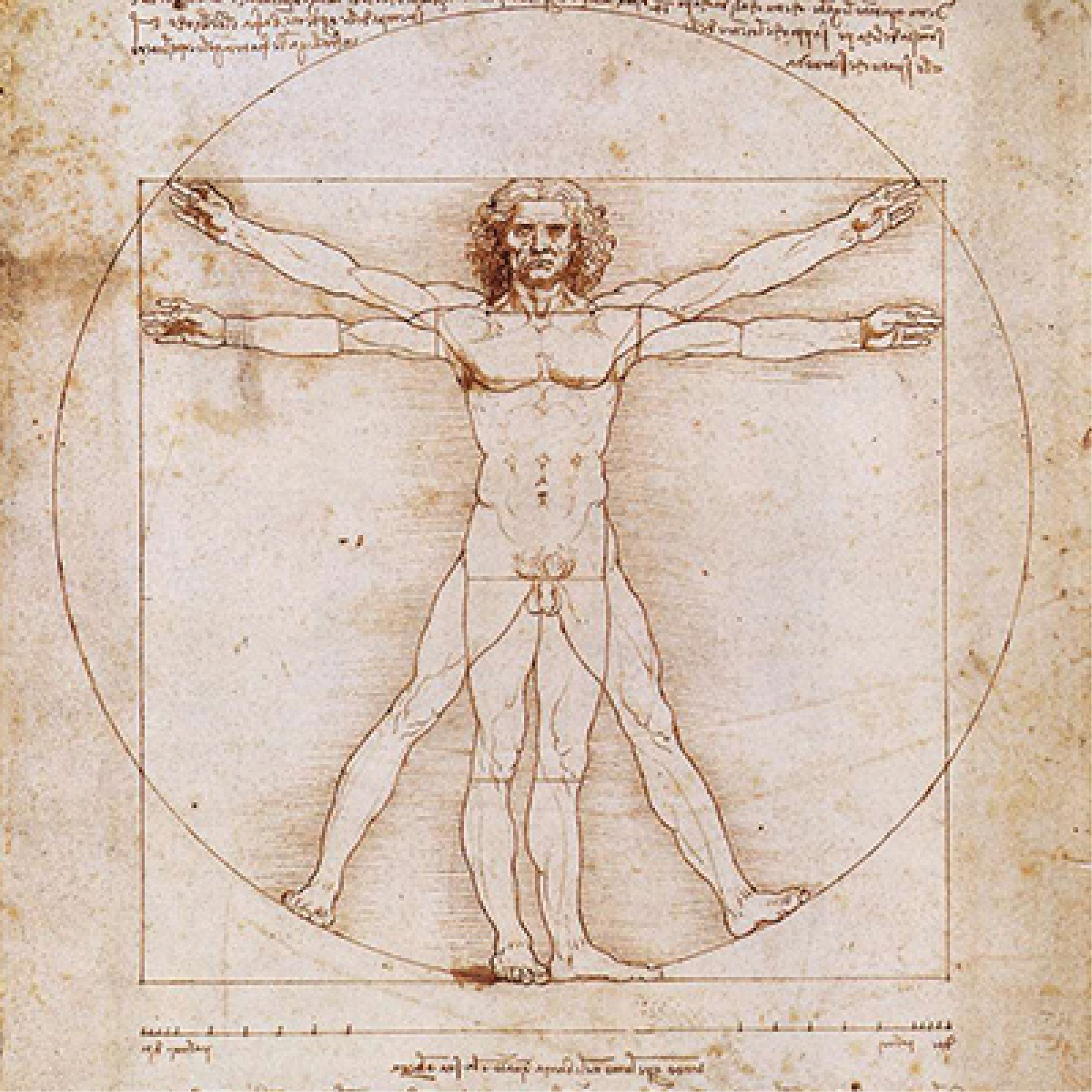
In an effort to diagram exactly what this could mean I created my facade as what may appear to be a simple collection of triangles, but upon closer inspection one can begin to notice that of the 10,770 triangles present in the shells design, no two are exactly alike.
Using Grasshopper scripting, I created a 'deffiniton' that divided my base geometry into a fractal like grid. calculating each face's size and sharpness to be determined based on factors such as opening portals, surface curvature, privacy, elevation and visibility. this developed further in a way that allowed points of compression in the structural shell to be come more evident in the overall pattern. the end result creates a grid-like system that challenges anyone to find a straight path along its edges.
In order to diagram the extents that robotic fabrication can go in creating unique forms, I used the size of the individual triangles to create an evolution of geometric changes as the scale of the face grows larger Stage 1: with closed faced units this step was parameterized to units too small to allow apertures on either side Stage 2: created dimples in units large enough to form openings but whose apertures would be too insignificant to allow in light or views. Stage 3: started to create hollow openings in units where the faces were large enough to bring in light or views Stage 4: began rotating the interior faces of units whose required edge thickness was less than 90% of the face's surface area. The greater the disparity, the greater the rotation. Stage 5: The largest and highest units were design to be fabricated using ETFE panels over a metal structure. This was used so that more natural light could be brought into the concourses. In addition to the amount of light, using ETFE means significant weight would be removed from cantilevering positions while the structure helps to tether the shell to the interior. It also achieves a two tone effect of materials on the buildings facade.
Fabrication
Because of the facade patterns destruction of significant linear paths, it was important that not only was robotic fabrication and assembly used at the smallest scale of the building's development. It needed to be carried through the entire process in order to reinforce the difference in robotic architecture's potential.
One important factor in this was establishing how the structural system of the facade would function. Because the triangular patterning disrupts all significant linear paths (apart from portal openings) there was no opportunity to create a traditional steel frame to support the units. Instead, using a system similar to that of Kraust's Breakwater Beacon Tower, I subdivided the overall geometry by surface area and curvature so that units could be individually printed as half shells, then arranged precisely on a sand bed where they could be fused together as a larger panel. these larger panels increase the structural capacity and allow for more openings than if units were fabricated individually like a system of brick
A system was designed to show how robotic precision would play a role in the final installation process. While this system depicts how it might be achieved using traditional robotic arms, it's also likely that equipment like cranes and scissor lifts will become outfitted with computer guided system and begin communicating with the larger robotic construction system.
Anomalies
Addressing the anomalies of the shell that fall outside the major robotic assembled pieces are actually some of the strongest instances of robotic architecture's impact o design. The four major openings in the building, acting as public vomitoriums, created an opportunity to relay even further how architecture can be influenced by robotics. The custom abilities of robotics go beyond the initial fabrication. the entrances for the building are given the opportunity to be fully customized using precision and material handling capabilities outside of human possibilities. This allows for a continuation of the overall "grid" inside the opening portals allowing for the architecture to both achieve a disruption of these inlets slicing their way into the facade, as well as a harmonious continuation in the larger triangular datum.
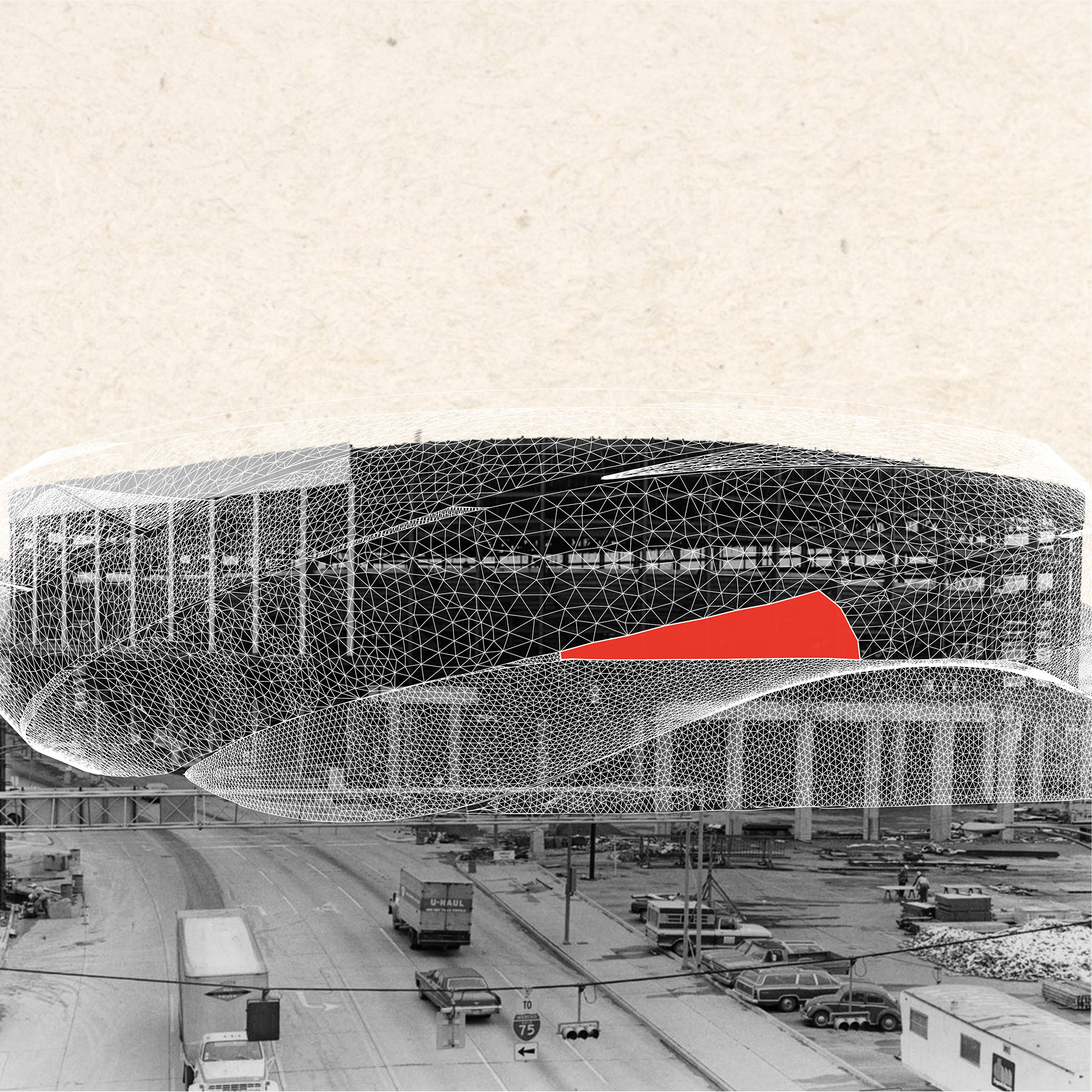
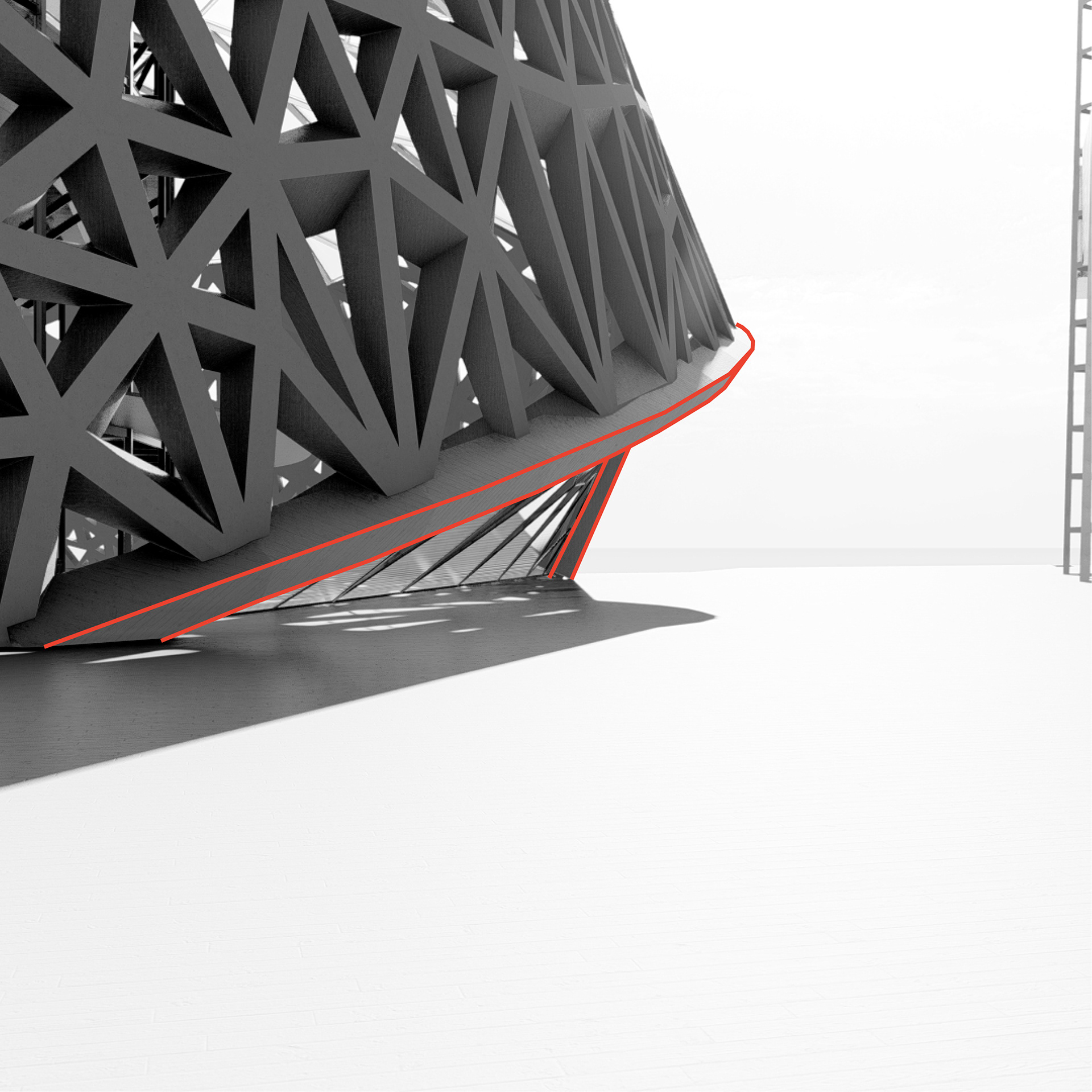
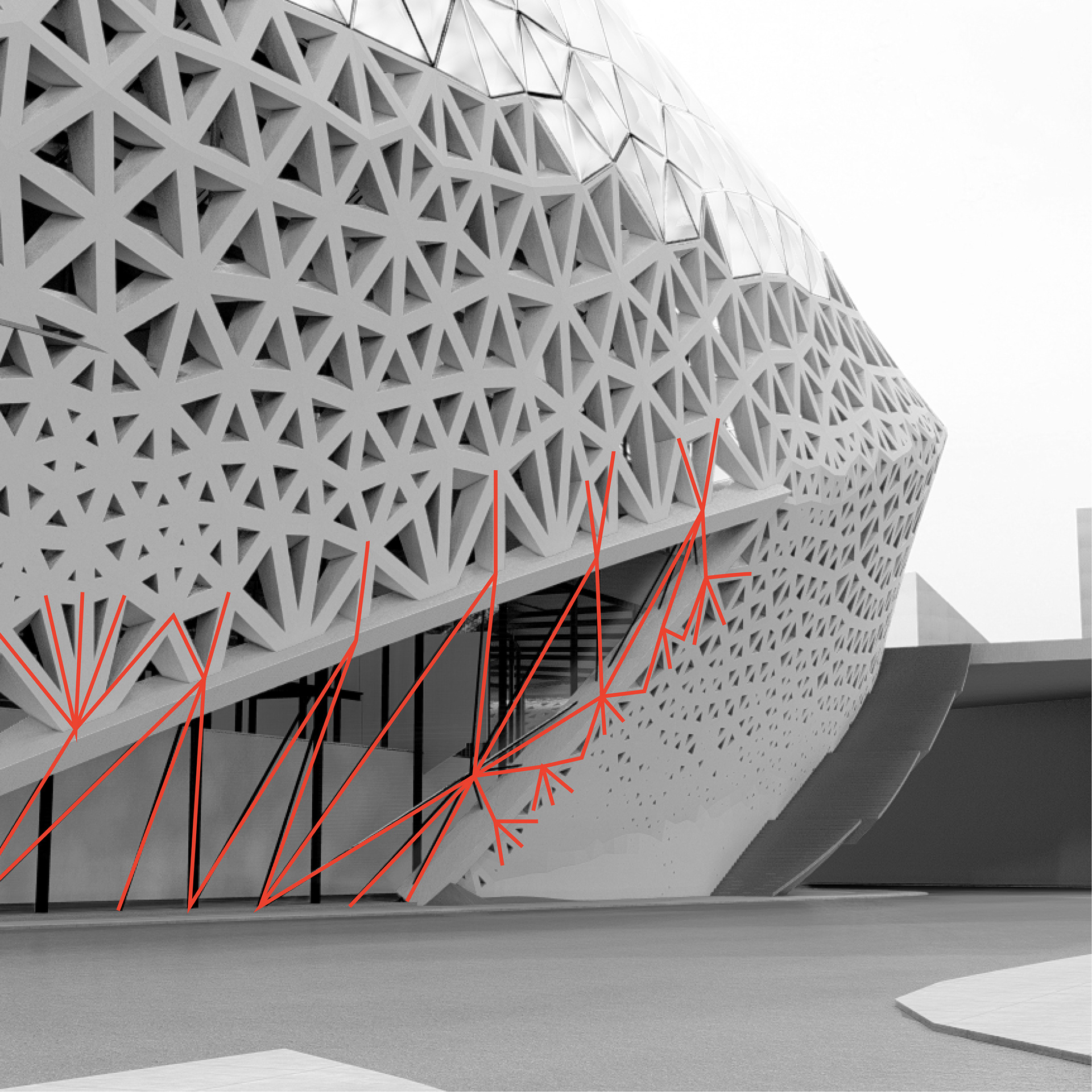
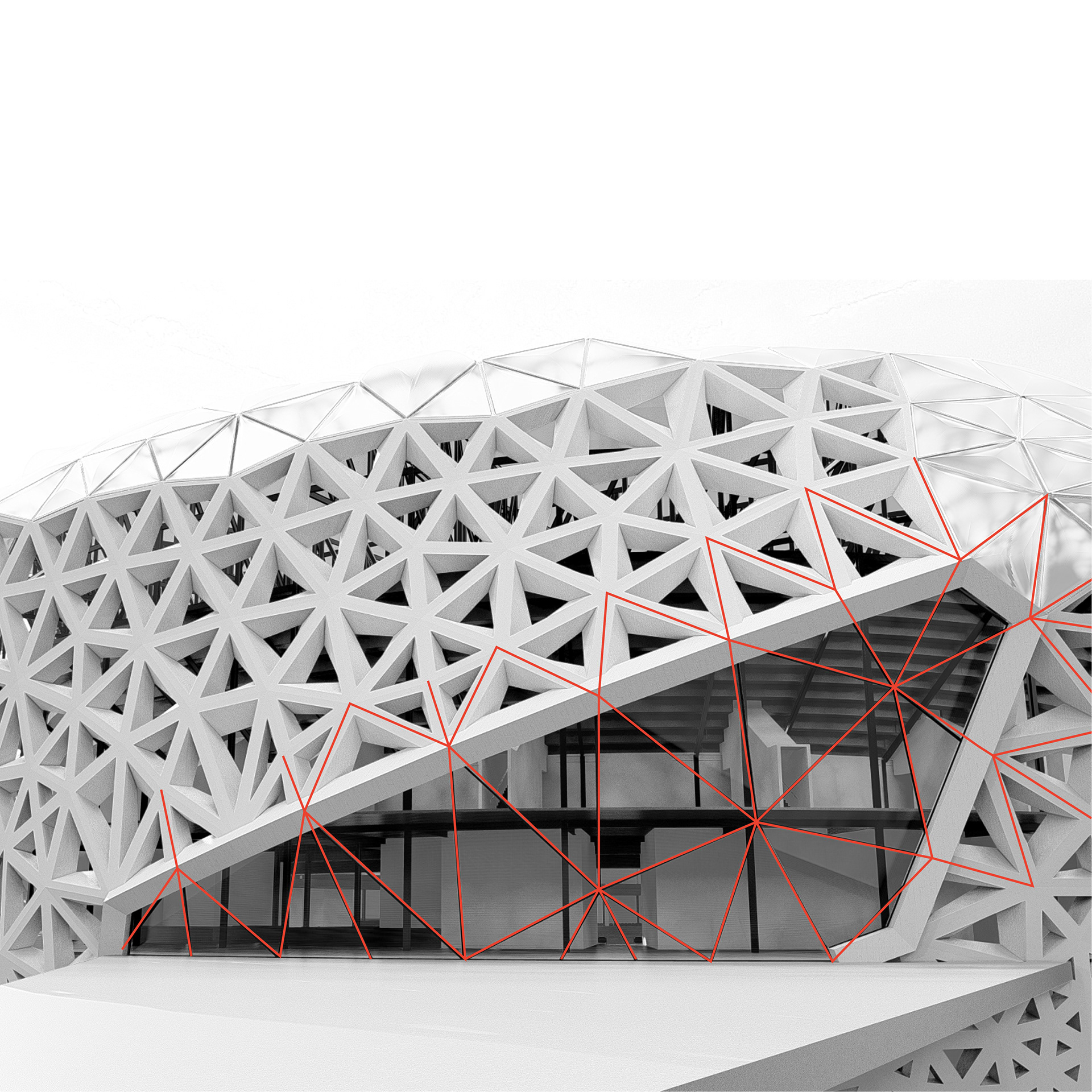
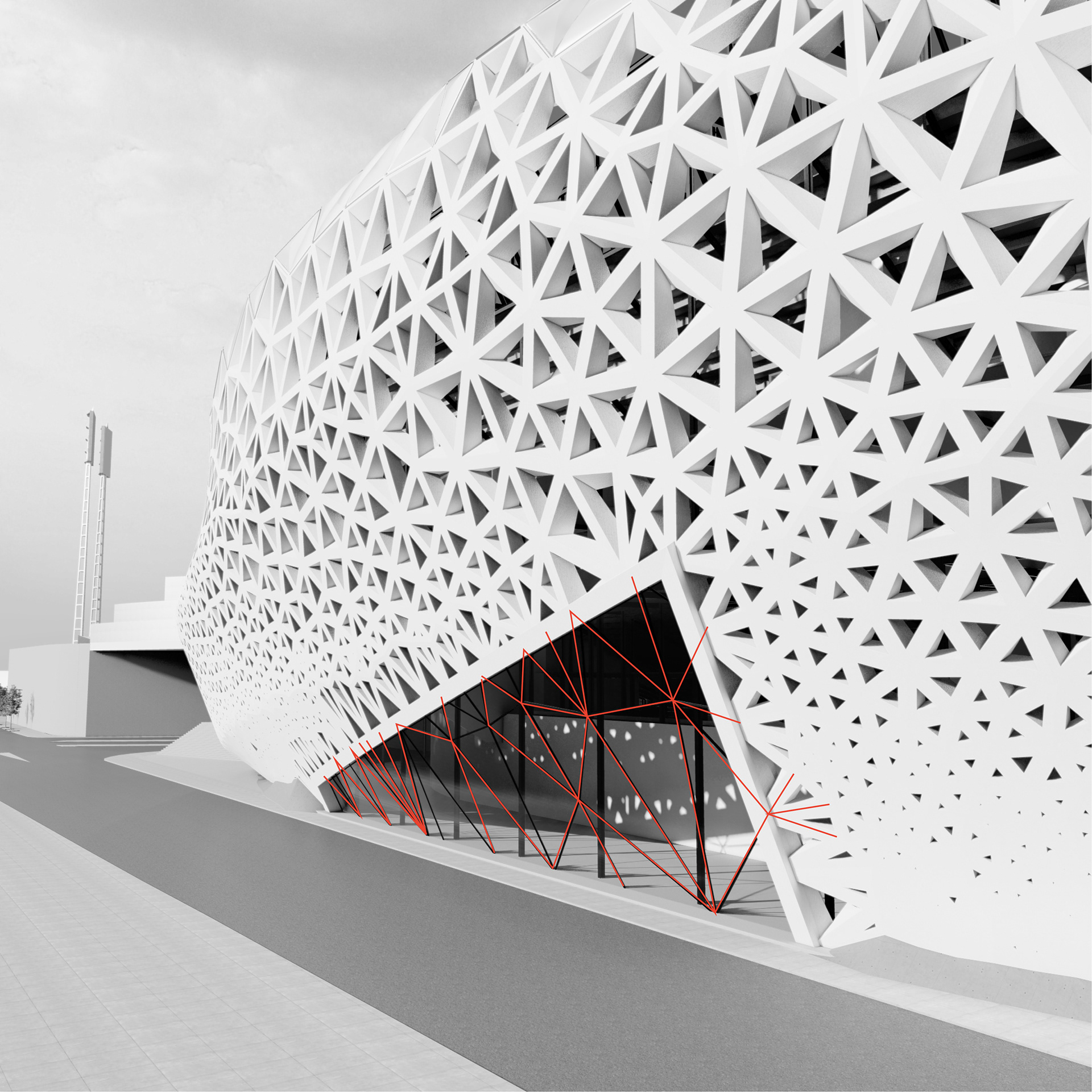
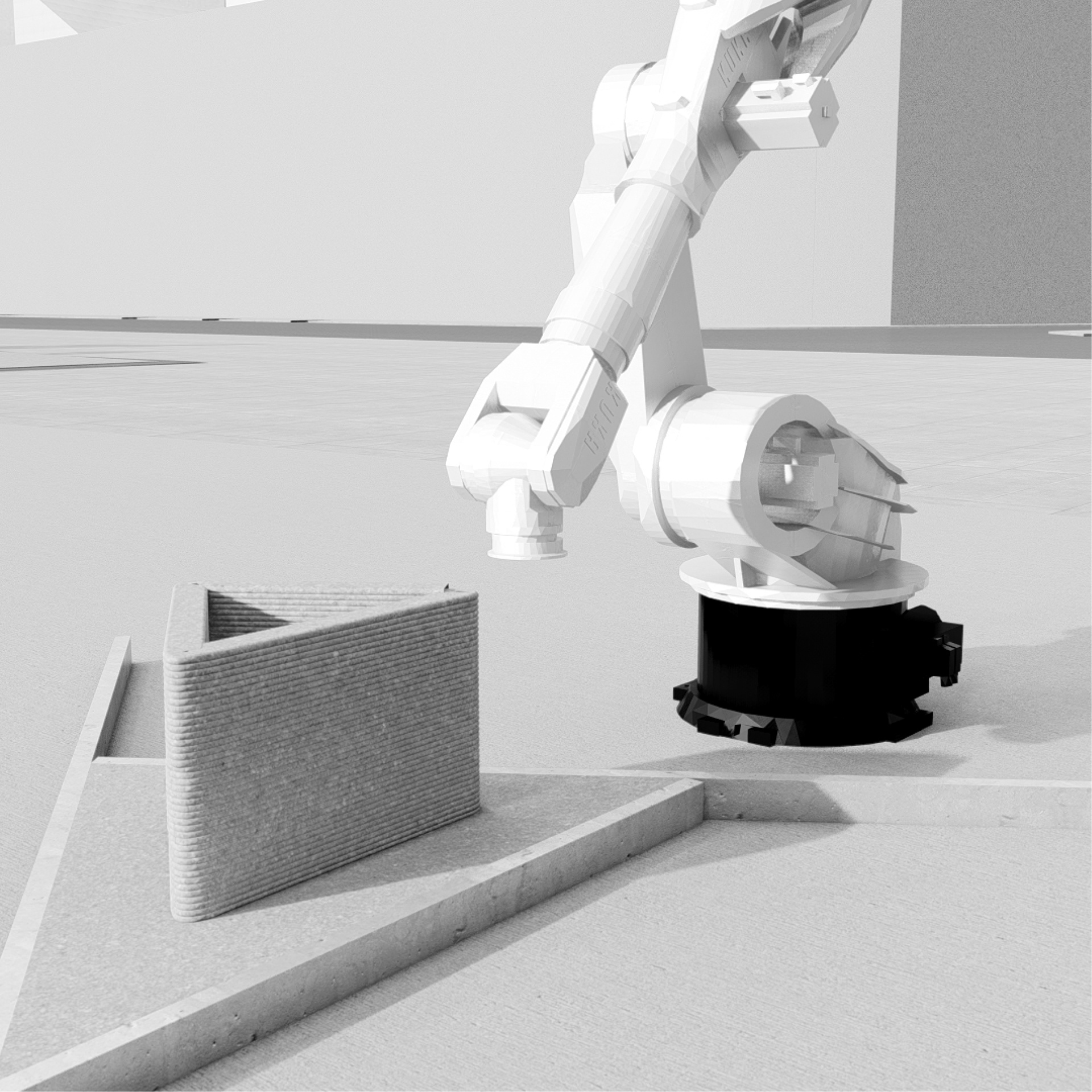
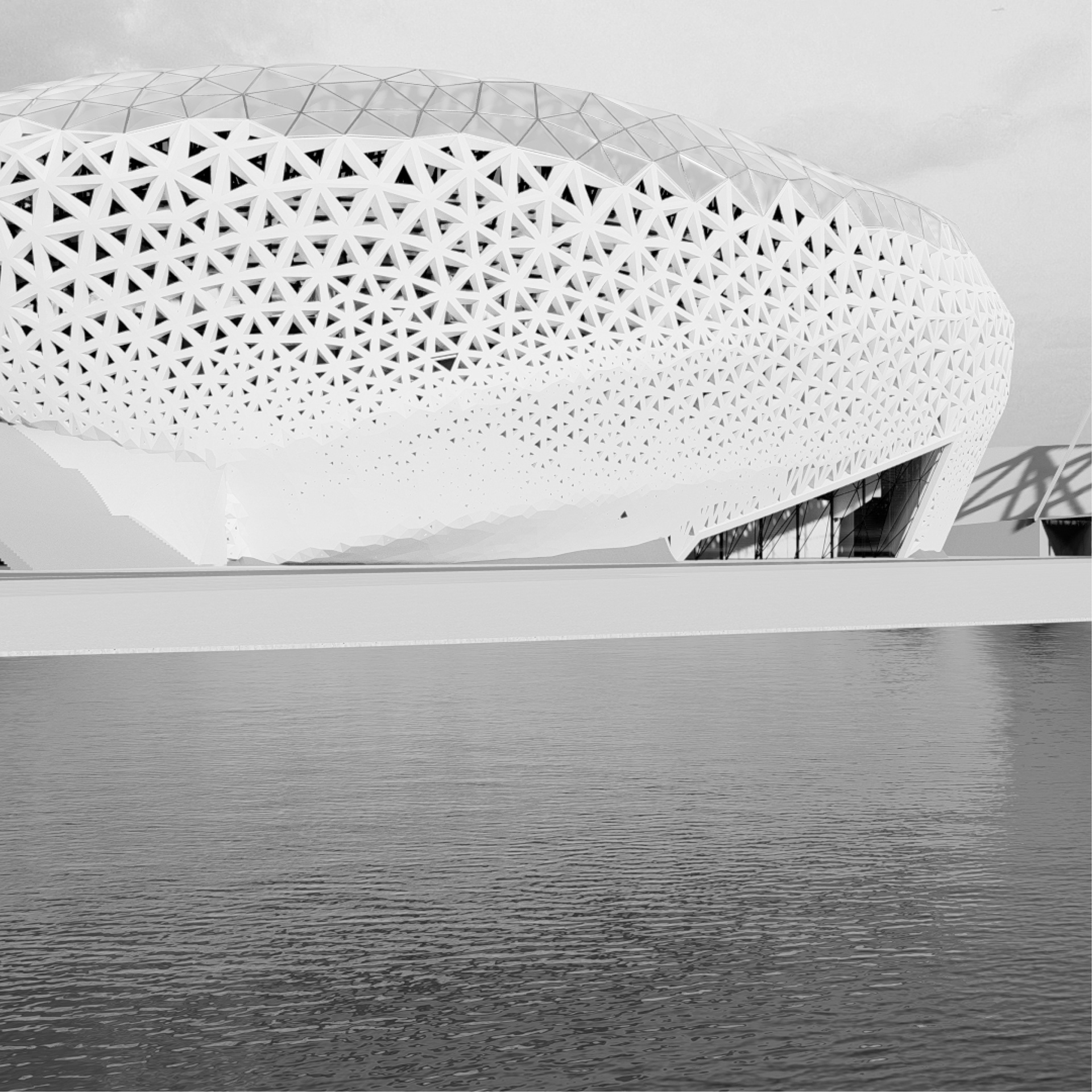
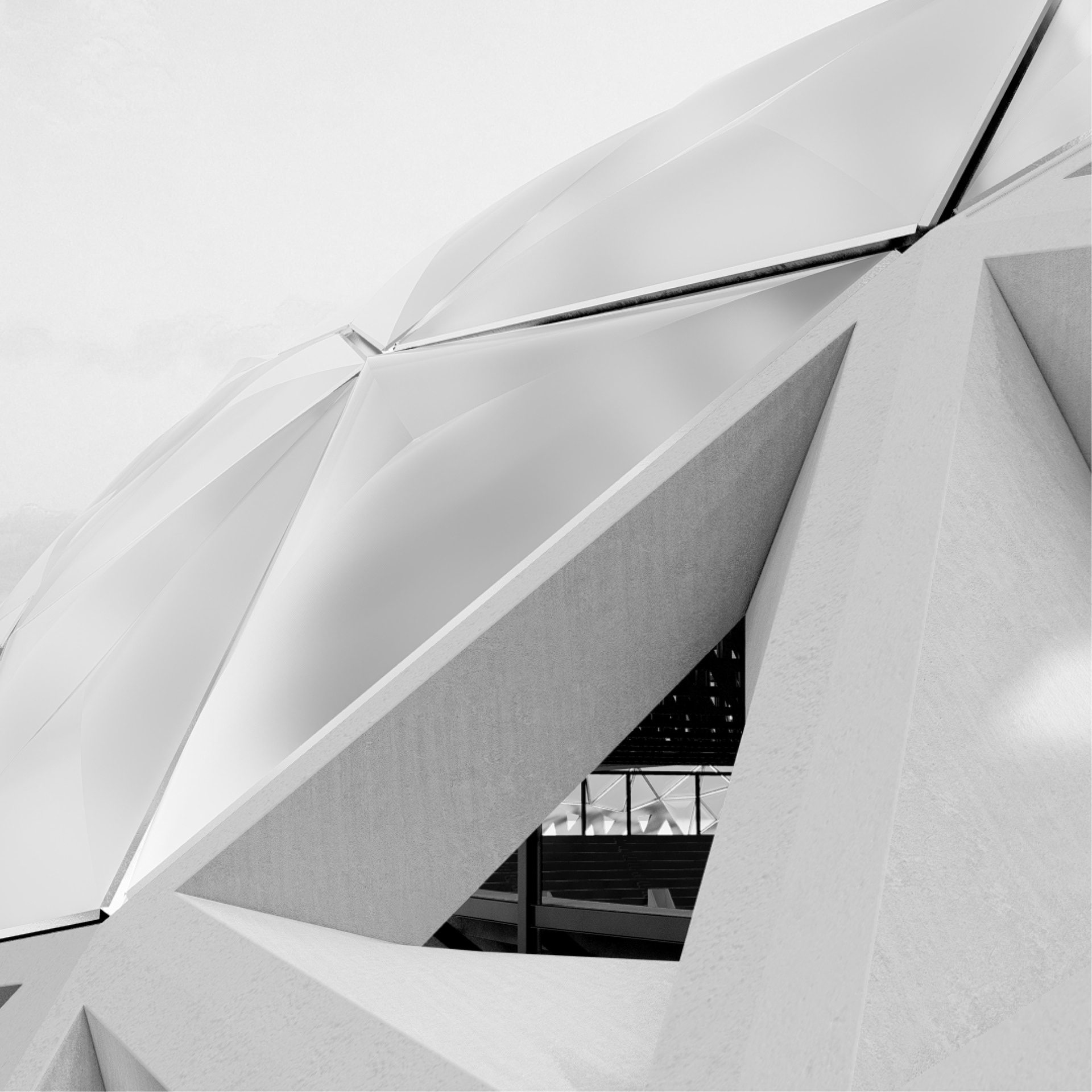
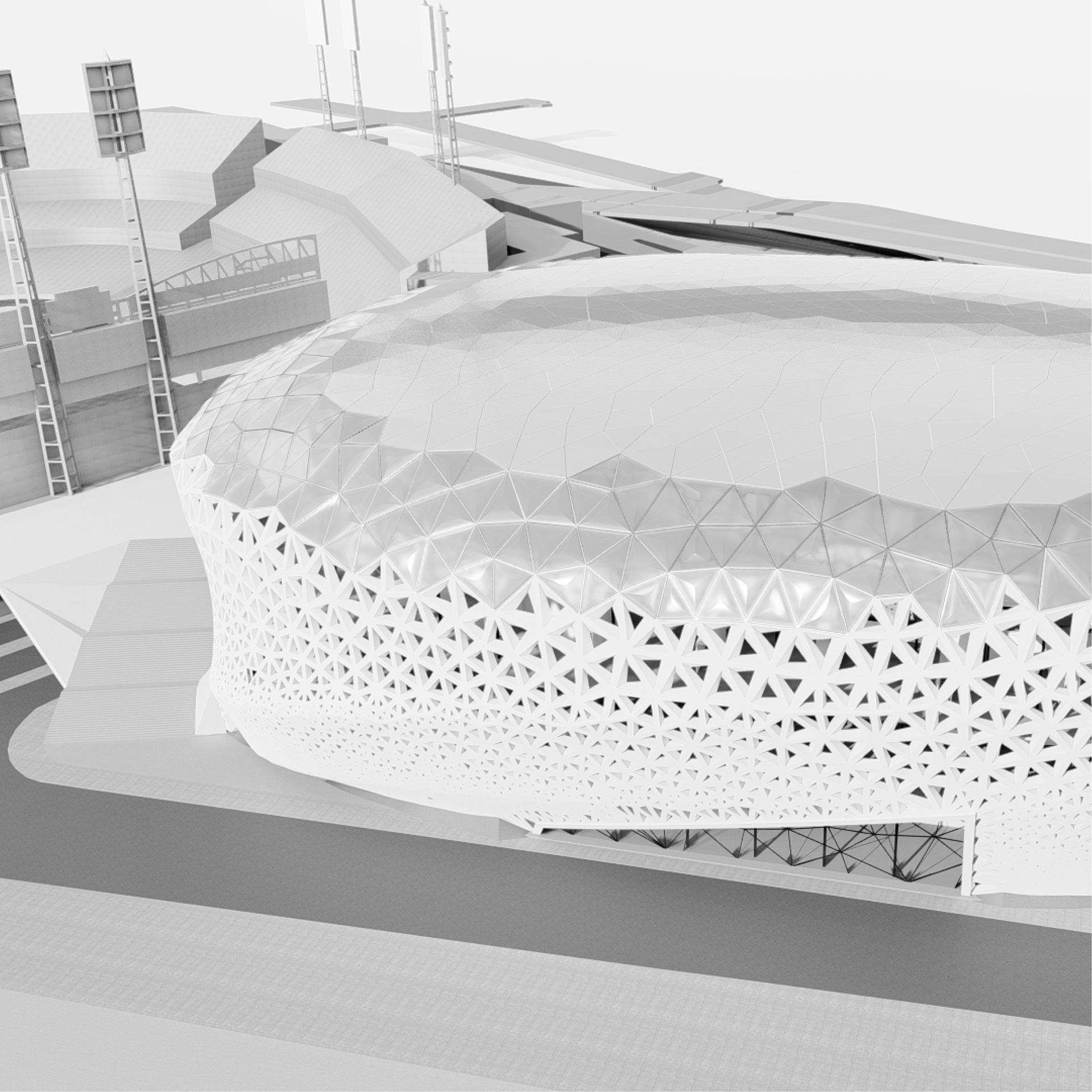